Direct Part Marking (DPM)
Direct Part Marking DPM is a process to permanently mark parts with a barcode.
The interpretation of 'permanent' often depends on the context the part is used. In the aerospace industry an aircraft part may be in service for over 30 years. Within telecom and computer industries the life cycle may only lasts a few years.
Direct Part Marking DPM is often used by automotive, aerospace, pharmaceutical, surgical instruments and electronic manufacturers to facilitate a reliable identification of their parts. This can assist in data logging for safety, warranty issues and satisfy regulatory requirements.
Also the United States Department of Defense demands a physical mark on tangible assets in conjunction with the Item Unique Identification.
They are many way to encode information to a machine-readable code. The preferred code are the Data Matrix and the QR Code. Data Matrix is used by Motorola. It is also preferred by NASA to mark parts. In the automotive industries also the QR Code is used. This is founded in the fact that this code was initially developed by Denso Wave (a global automotive components manufacturer) for tracking parts in vehicle manufacturing.
Direct Part Marking Solutions - DPM
Tracking individual components can be a costly proposition when standard product labelling techniques fail to measure up over time. Direct Part Marking - DPM provides a permanent marking solution that ensures readability throughout the life of your products, even when subjected to harsh environments during the manufacturing process.
Meet traceability requirements imposed by regulatory and government entities, such as the U.S. Department of Defence, with high-performance DPM readers from Motorola's cost-effective alternative to standard vision systems.
Enjoy flexibility and performance.
Give your production line and quality teams the flexibility they need to read DPM when and where they need to, while performing a variety of other tasks. Available in multiple form factors - a handheld or fixed-mount scanner, or a rugged mobile computer - Motorola DPM Readers read a wide variety of marks, including:
- dot peening
- laser etching
- chemical marking
- molding
- casting methods
- Abrasive blasting
- Adhesive dispensing
- Cast, forge or mold
- Scribe
- Electro-chemical etching
- Embroidery
- Engraving/milling
- Laser marking
- LaserShot peeing
- Stencil (mechanical cut, photo process, laser cut)
On multiple substrates, including:
- metal
- plastic
- glass
Minimize investment and process changes.
Track, monitor and manage parts ranging in value from pennies to millions of dollars with minimal investment or process change. Maximize production efficiency while leveraging the same DPM product investment to perform quality, warehouse and other line-side functions. Much less complex than traditional vision systems, Direct Part Marking solutions from Motorola are rapidly deployable with minimal user training.
Key benefits that can be realized include:
- Increased worker productivity
- Streamlined data collection
- Improved data accuracy
- Improved product quality
- Cost-effective compliance with traceability regulations
Direct Part Marking (DPM)
Tracking individual components can be a costly proposition when standard product labelling techniques fail to measure up over time. Direct Part Marking (DPM) provides a permanent marking solution that ensures readability throughout the life of your products, even when subjected to harsh environments during the manufacturing process.
There are many business benefits to the implementation of Direct Part Marking:
- True "Cradle to Grave" traceability of product
- Improvement of Manufacturing Processes
- Identification of quality defects throughout the Manufacturing Process
- Eliminates Manual Data Entry and therefore Human Error
- Supports Data Logging and Automatic Data Collection
- Consequently reducing the overall cost of manufacturing
Initially, the code has to be marked in some way and the method is dependant on the material to be marked, the required lifespan of the mark, the accessibility of the area to be marked, production speed / volume etc. The most common methods of marking are Laser-etching, Dot peening, Ink-jetting and Chemical-etching.
Verification
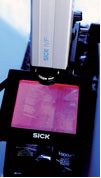
Verification is required in many instances to check the quality of code, particularly at time of marking. This can provide immediate feedback as to any changes to the marking process. For example, the verifier can monitor tip wear on a dot peen machine by monitoring dot size, and flag the operator.
At the marking stage, during the manufacturing process and throughout the products lifecycle, the mark will be required to be read. Depending on the situation and the environment, this could be with a handheld reader tethered to a host computer or with a remote Bluetooth connection.
The information could be gathered with a Mobile Computer with inbuilt reader and wirelessly transmitted back to the host. Fixed Position readers are used for automatically collecting the data on some form of automated transfer or a presentation type reader used in an application where the user needs to be "hands-free".